All-solid-state batteries | Applications and collaborations case studies
Solving issues in factory automation | ||
Contributing to reducing maintenance man-hours and improving productivity for industrial robots/servo motors |
Background
In recent years, there has been a growing demand for automation and efficiency in relation to industrial robots. Further, industrial robots are rapidly evolving with the introduction of AI, the popularization of collaborative robots, improved safety due to improved sensor technology, energy saving, edge computing due to integration with IoT, environmental considerations, etc.
Batteries are used for the backup power supply of the sensor (encoder) that detects the rotation angle, such as in the joints of industrial robots; however, existing batteries have restrictions in use at high temperature and maintenance associated with battery replacement needs to be implemented frequently, so there is a need for longer battery life.
Issues
(1) Downsizing and heat resistance required for parts of industrial robots
To improve productivity, it is necessary to accelerate the operating speed of industrial robots as well as the downsizing and weight saving of the parts used in robots. As the temperature of rotating mechanisms such as servo motors increases due to faster operation, heat resistance is required for these parts. In manufacturing processes in high-temperature environments such as heat-press processing, further heat resistance is required.
(2) Reduction of maintenance man-hours for industrial robots
The servo motors used in multi-axis robots are equipped with encoders that control the position. The encoders record data such as position and angle when the robot stops, and restart operation when the robot restart using the data. For the encoders, primary batteries (single-use type) are generally used when backing up such data; however, if the battery capacity is insufficient, the robot will become inoperable, so periodical battery replacement is necessary.
In situations where there are concerns about labor shortages, there is a growing demand for maintenance-free systems as more and more robots are utilized, and the development of long-life batteries is required.
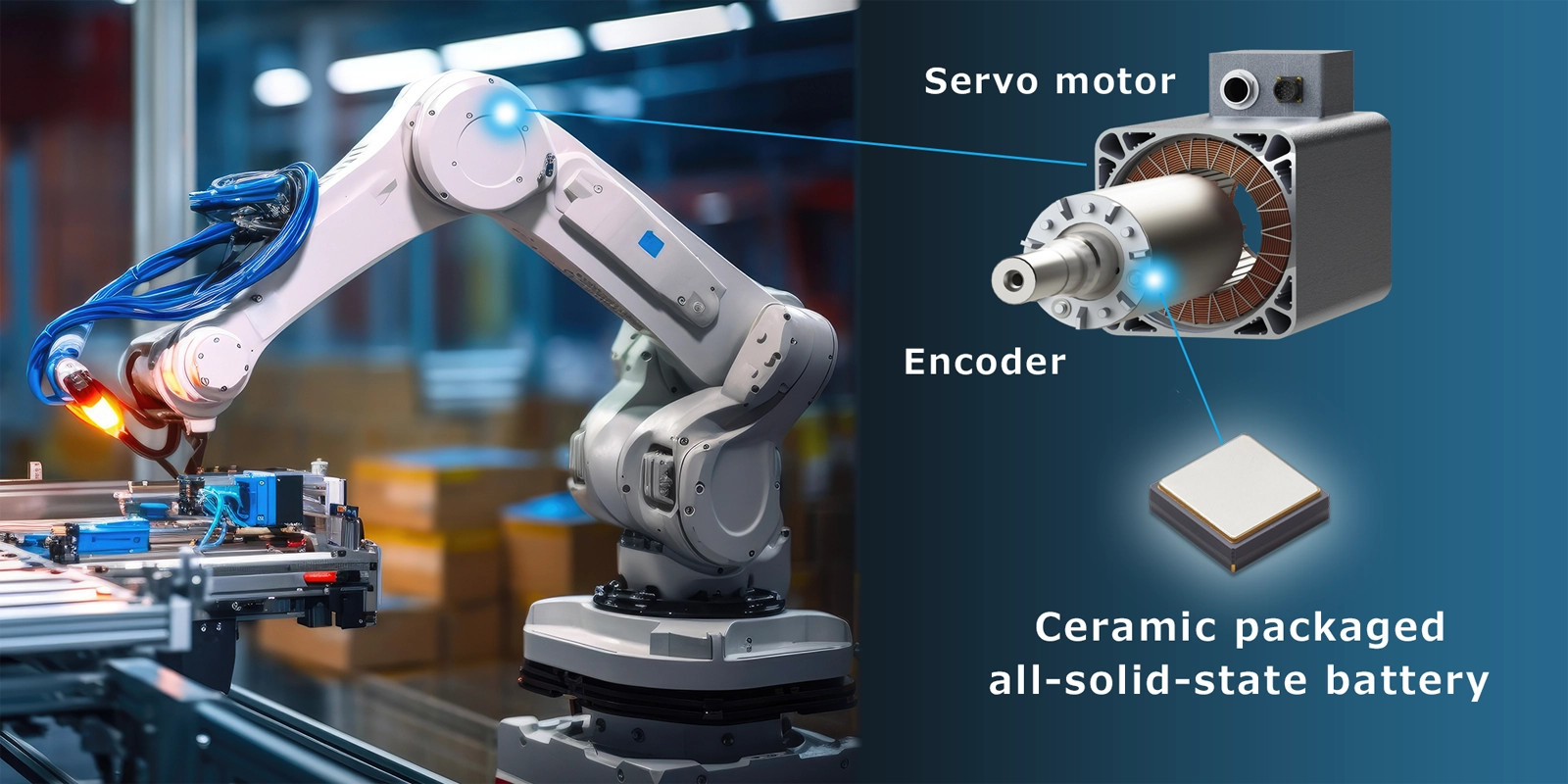
Image of a servo motor installed in the rotating part of robot and an encoder embedded in it
Solution
To solve these issues, by adopting all-solid-state batteries, which are more heat resistance than primary batteries conventionally used in encoders, can be used under harsh conditions at high temperatures∗1 with long-life characteristic∗2, contributing to the realization of a maintenance-free∗2 society in a wide range of fields. Moreover, while conventional industrial robots have a backup battery outside the main body via a harness, the integration of the all-solid-state battery, encoder, and servo motor eliminates the need for a harness, contributing to the miniaturization of robots.
- Under harsh conditions at high temperatures: It is possible to discharge up to 125 deg. C. The heat resistance is high compared to that of general lithium-ion batteries.
- Long-life characteristics and maintenance-free: The Maxell conventional coin-type lithium-ion battery (927 size) can maintain 90% capacity for 10 days, while the all-solid-state battery can maintain 90% capacity for 100 days, based on accelerated testing at 60 deg. C.
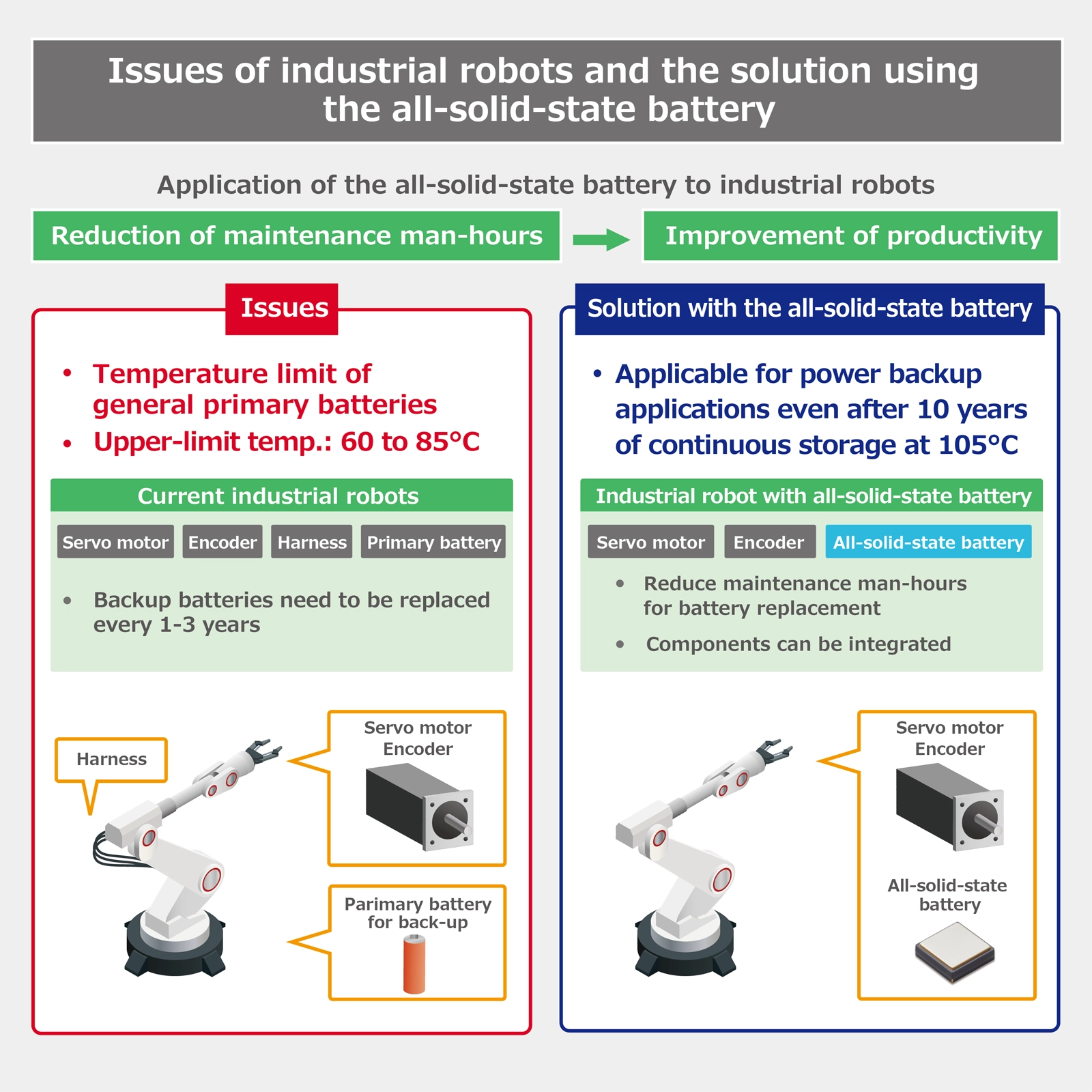
Adoption case studies
Other applications
